Unlocking Precision
The Power of 3D Laser Scanning Integrated with 3D CAD
in Metal Fabrication
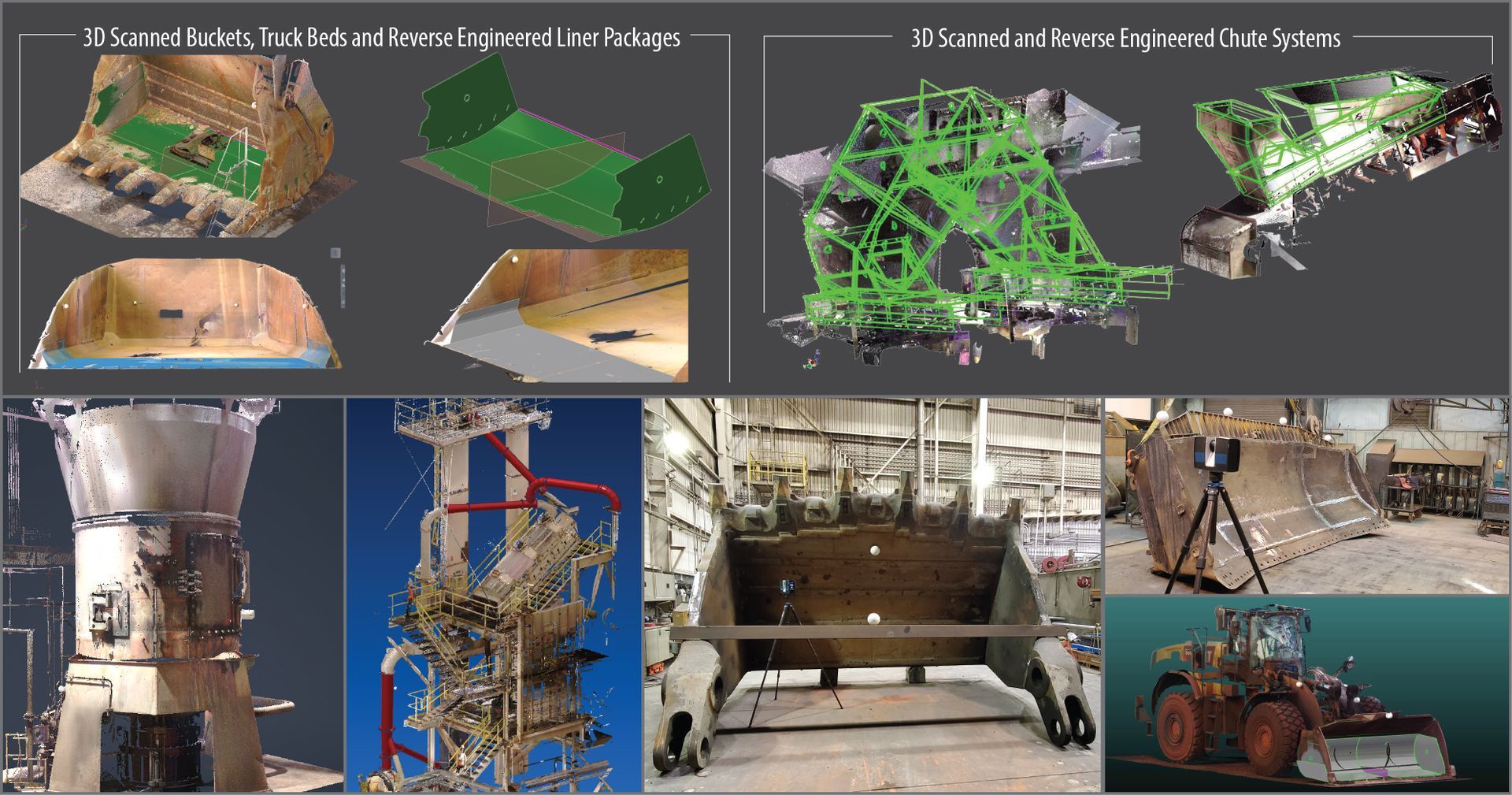
After 70+ years in the metal fabrication industry, SAS Global has seen countless technological advancements come and go. But few innovations have made as profound an impact on accuracy, efficiency, and engineering design as the integration of 3D laser measurement scanning with 3D CAD software.
Whether you're working on wear liners, material handling systems, or custom-fitted components, time in the field is valuable, and the margin for error is razor-thin. This is where 3D laser scanning transforms the game.
The Next Generation of Measurement
Traditional hand measuring, while reliable in its time, is labor-intensive and leaves room for human error. Measuring a loader bucket, for example,
used to take a couple of hours, now it takes
15 minutes or less with a modern
3D Laser Scanner.
Each scan captures
millions of data points, all mapped precisely in three-dimensional space. These data points form what's known as a "point cloud," essentially a digital twin of your existing component or system. This model can then be imported into CAD software, giving engineers a visually navigable and dimensionally accurate representation to work from.
Why This Matters in the Field
Here are some of the most significant advantages SAS has experienced firsthand:
- Substantial Time Savings: Measuring time is slashed dramatically, reducing labor costs and expediting project timelines.
- Unmatched Accuracy: With a measurement tolerance of less than 1/32" on smaller components and 1/32" to 1/16" on large system scans, the precision surpasses what’s achievable by hand.
- Scalability: There's virtually no size limitation. Large systems, from chutes to full processing lines, can be captured using multiple overlapping scans.
- Perfect Fit, Every Time: Integrating scan data directly into 3D CAD allows for the creation of perfectly contoured components and liners. This eliminates guesswork and dramatically reduces rework or field adjustments.
Enhancing Engineering and Fabrication Workflows
Once imported into CAD, the point cloud becomes the foundation for highly accurate reverse engineering, clash detection, or component redesign. You’re not just working from measurements—you’re working from reality.
Design modifications are now based on an exact replica of the real-world component, which means:
- Faster design cycles
- Improved product quality
- Greater confidence in fabrication tolerances
- Fewer fitment issues in the field
Final Thoughts
In today's high-demand, precision-driven fabrication industry, there's little room for inefficiency. By combining the capabilities of advanced
3D Laser Scanners with powerful CAD modeling tools, we're not just improving how we measure, we are revolutionizing how we design, fabricate, and install.
It’s not just about capturing what’s there. It’s about building what fits perfectly.
Contact SAS Global today to discuss your scanning, engineering, and custom metal fabrication needs.