The Importance of Selecting the Proper Wear Resistant Material for Your Application
Why Proper Wear Resistant Material Selection Matters
Why Material Selection Matters
In heavy industrial environments, wear and tear are inevitable, but premature equipment failure doesn’t have to be. Selecting the proper wear-resistant material can dramatically extend service life, reduce maintenance costs, and increase production uptime. The wrong choice, however, can result in excessive downtime, higher operating costs, and unplanned outages.
At SAS Global Corporation, we’ve engineered and field-tested a full spectrum of premium materials that meet the unique wear challenges across industries like mining, power generation, steel production, and aggregate handling.
Understanding the Types of Wear
Wear generally falls into three primary categories:
1. Abrasive Wear
Caused by hard particles or rough surfaces sliding across a material—this is the most common type of wear in mining, cement, and power generation applications.
2. Impact Wear
Occurs when materials experience repeated high-force contact, such as in crushers or heavy hammer mills.
3. Erosive Wear
Caused by fine particles carried by air or liquid streams impinging on surfaces—common in coal handling ducts, fan blades, and piping systems.
What Happens When You Select the Wrong Wear-Resistant Material?
Choosing the wrong wear-resistant material for your application doesn’t just lead to underperformance—it can cause significant operational, financial, and safety issues. Below are common and costly consequences:
1. Premature Wear and Failure
What happens:
If the material lacks the necessary hardness or toughness, it will wear out much faster than expected.
Example:
Using AR400 plate in a high-abrasion coal chute may lead to through-wear in 2-3 months, whereas SA6000 would last over a year.
Impact caused to your operation:
- Frequent replacements
- Increased labor costs
- Downtime for unscheduled maintenance
2. Cracking or Spalling
What happens:
In high-impact environments, a hard but brittle material (like a ceramic tile) may crack or shatter upon repeated shock loading.
Example:
Applying ceramic in a primary crusher liner where impact is severe may lead to cracking and material failure. A better choice would be Vanguard Alloy Wear Plate, which is engineered to handle impact.
Impact caused to your operation:
- Risk of material failure during operation
- Potential equipment damage
- Compromised safety
3. Material Buildup and Flow Issues
What happens:
Rough or improperly finished surfaces trap sticky materials like clay, wet coal, or biomass, leading to flow blockage or bridging.
Example:
Standard alloy wear plate in a biomass chute causes daily plugging, while RapidFlow eliminates carryback with its smooth finish.
Impact caused to your operation:
- Manual intervention and cleanup
- Lower throughput and productivity
- Increased risk of material spills or downtime
4. Over-Engineering = Wasted Cost
What happens:
Using a premium wear material where a basic alloy would suffice results in unnecessary spending with no added benefit.
Example:
Using SA6000 in a low-wear bin liner that could easily handle SA400 or AR400.
Impact caused to your operation:
- Inflated project costs
- Ties up budget that could be used elsewhere
- No meaningful improvement in service life
5. Compromised System Performance
What happens:
Misaligned wear material properties (e.g., too soft, too brittle, wrong surface energy) can cause issues like:
- Airflow turbulence
- Slurry cavitation
- Misaligned tolerances
Impact caused to your operation:
- Lower efficiency
- Increased power consumption
- Component mismatch and failure propagation
Summary: A Poor Material Choice is Expensive
Issue | Common Result | Corrective Action |
---|---|---|
Under-spec’d material | Frequent failure | Upgrade to harder or tougher material |
Over-spec’d material | Wasted money | Reevaluate with real wear data |
Wrong surface finish | Flow issues | Use smooth finish overlays |
Wrong wear mechanism | Acelerated Wear - Cracking/spalling | Match to impact or abrasion type |
Matching the Right Material to the Wear Type
For Abrasive Wear (high hardness, low impact)
Application Examples: Coal mill liners, hoppers, chutes, fan housings, classifier cones
Suggested Wear Materials:
- SA1750CR: Premium Chromium Carbide Overlay
- SA2000: Premium Complex Carbide Overlay
- SA6000: Patented Microstructure Complex Carbide Overlay
- RapidFlow: Smooth Surface Finish CCO
Why: These materials have high hardness (58–65 HRC) and a dense carbide structure that resist material loss from sliding or gouging.
For Impact Wear (moderate to high impact, moderate abrasion)
Application Examples: Crusher liners, impact bars, hammers, buckets
Suggested Wear Materials:
- Vanguard: Premium Alloy Wear Plate (500 Brinell)
- SA5502NM: 11-14% Work-Hardening Manganese Steel
- SA400: Alloy Wear Plate (400 Brinell)
Why: These plates provide toughness and ductility, essential for absorbing repeated impact energy.
For Combined Abrasion + Impact
Application Examples: Screen plates, dragline buckets, discharge chutes
Suggested Wear Materials:
- SA6000: Patented Microstructure Complex Carbide Overlay
- SA2000: Premium Complex Carbide Overlay
- Vanguard: Premium Alloy Wear Plate (500 Brinell)
Why: These materials strike a balance between surface hardness and structural strength, giving you abrasion resistance without being brittle under impact.
For Erosive Wear (fine particle impingement at angles)
Application Examples: Cyclone separators, coal pipes, elbows, dust collectors, fan blades
Suggested Wear Materials:
- SA6000: Patented Microstructure Complex Carbide Overlay
- SA2000: Premium Complex Carbide Overlay
- RapidFlow: Premium Smooth Surface Carbide Overlay
Why: The refined micro-structures of SA2000 and SA6000 provide maximum protection from fine particulate wear. Smooth overlays like RapidFlow reduce turbulence and directional wear caused by particle streamlines.
For Sticky or Moist Materials (carry back, buildup, plugging)
Application Examples: Truck bed liners, transfer chutes, coal handling, biomass conveyors, pugmills
Suggested Wear Materials:
- RapidFlow: Premium Smooth Surface Carbide Overlay
Why: Sticky materials (e.g., wet coal, clay-laden ores, wood ash) tend to accumulate on rough or uneven surfaces, causing:
- Plugging and buildup
- Flow restrictions
- Increased maintenance time
- Reduced throughput
RapidFlow addresses this problem by combining
abrasion resistance with a
high-polish, ultra-smooth surface finish. This reduces the surface energy and friction coefficient, making it significantly harder for material to stick or cake. Compared to traditional chromium carbide overlays,
RapidFlow can reduce carryback by up to 80% in field trials.
Key ROI Benefits:
- Reduced downtime = More uptime hours annually
- Lower replacement frequency = Fewer labor costs
- Increased system efficiency = Reduced energy consumption (especially in flow systems)
Final Thoughts: Don’t Guess—Engineer
The material you choose should be based on actual wear data, impact stress, environmental conditions, and economics. At SAS Global, we use
lab-tested, field-proven methodologies to recommend materials that deliver
maximum performance and ROI. No guesswork, just engineered solutions.
The
key takeaway is that wear-resistant materials are not “one size fits all.” Success comes from
engineered selection—matching material properties precisely to the wear mechanism, load condition, and operating environment.
SAS Global’s wear specialists can help you avoid these pitfalls with field-backed recommendations that improve ROI and eliminate guesswork.
Ready to Improve Wear Life?
Visit our Premium Wear Materials Page or reach out for a wear analysis and material selection consultation.
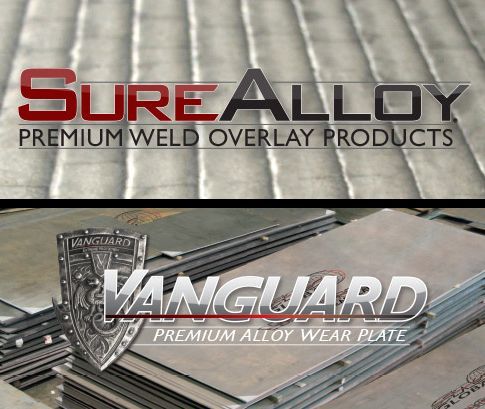