The Hidden Power of a Smooth Premium Haul Truck Bed Liner
Boost Production, Cut Costs, and Enhance Safety—One Dump Cycle at a Time
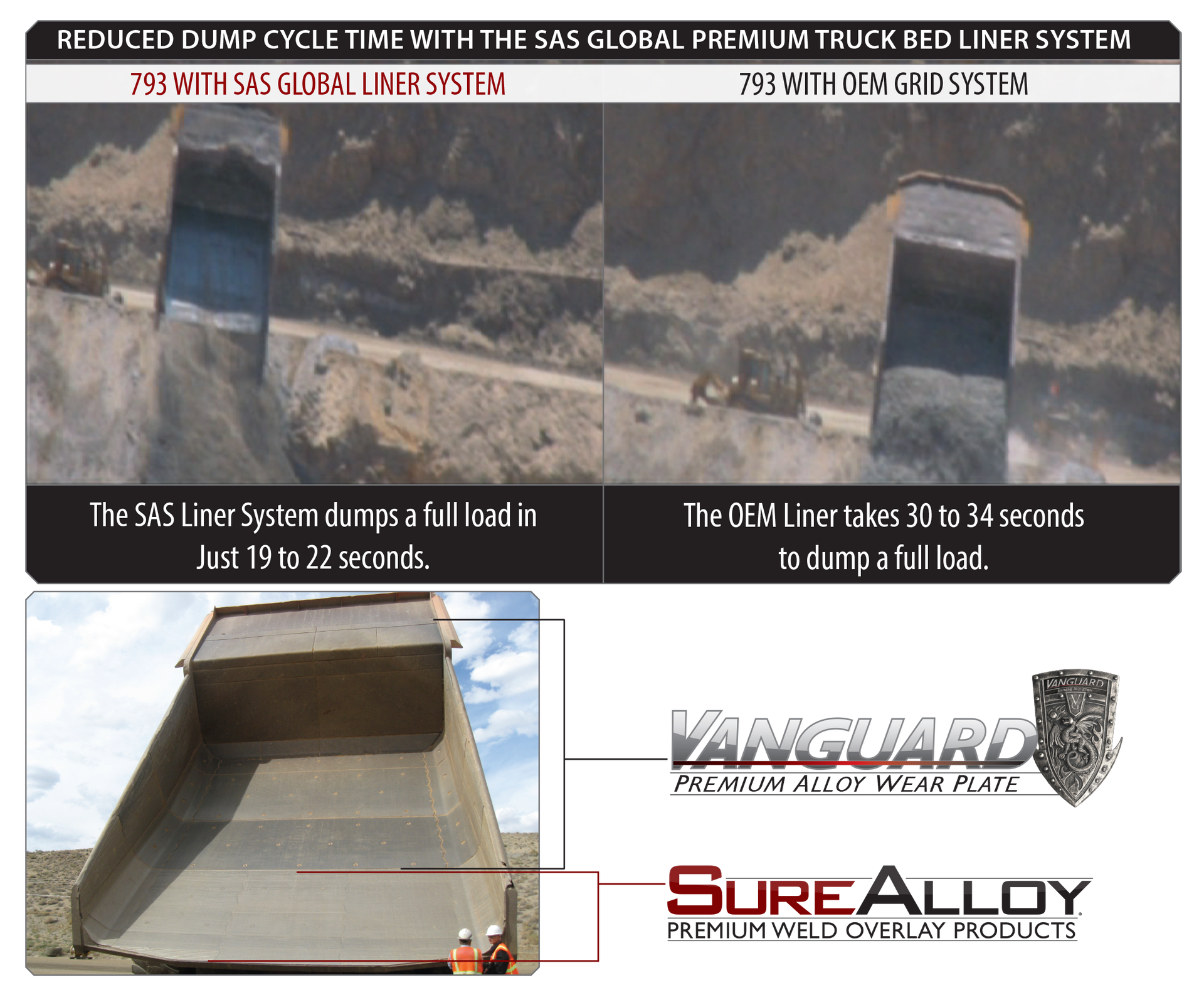
In the demanding world of mining operations, efficiency and safety are paramount. One often-overlooked component that significantly contributes to these factors is the haul truck bed liner system. Implementing a well-engineered, smooth liner package can lead to substantial improvements in production rates, equipment longevity, and worker safety.
Accelerated Dump Cycles Boost Productivity
A smooth liner facilitates quicker and more complete material release during dumping. For instance, SAS Global's Premium Truck Bed Liner System enables a full load to be dumped with the bed raised to only 70%, reducing cycle times by approximately 10 to 15 seconds per load. In a fleet of 15 trucks handling between 280 to 300 loads per shift, this time savings accumulates to an additional 45 to 50 minutes per shift. Over two shifts, this efficiency translates to hauling an extra 2 to 3 loads daily, amounting to approximately 273,000 additional tons annually.
Enhanced Equipment Longevity and Reduced Maintenance Costs
By allowing material to be dumped with the bed raised only to 70%, the strain on hydraulic lift cylinders is significantly reduced. This decrease in mechanical stress minimizes wear and tear, leading to fewer breakdowns and lower maintenance costs. Moreover, smoother liners reduce carryback—the residual material that sticks to the bed—ensuring that trucks operate at their full designed capacity without unnecessary weight. This not only improves fuel efficiency but also decreases the frequency of maintenance interventions.
Improved Safety and Increased Payload Capacity
Material sticking in the corners of haul truck beds poses significant safety risks, especially during maintenance when residual material can dislodge unexpectedly. A smooth liner minimizes material adhesion, thereby reducing the risk of injury to maintenance personnel. Additionally, less carryback means that each load transported is closer to the truck's maximum payload capacity, enhancing overall operational efficiency.
Return on Investment: Quantifying the Benefits
The financial implications of installing a smooth liner are compelling. Consider a mining operation with a fleet of 72 haul trucks. By reducing underloading and ensuring each truck carries its full capacity, the operation can significantly decrease the number of trips required, leading to substantial fuel savings. For example, eliminating 15 unnecessary trips per day can result in nearly $1.9 million in annual savings per truck over 250 operating days.
Furthermore, studies have shown that optimizing dump cycles and reducing engine idling time during dumping can lead to significant fuel savings. A recent case study revealed that minor modifications to operator behavior during the dumping cycle resulted in annual fuel savings of up to 275,000 liters for a fleet of 72 trucks.
In conclusion, investing in a well-engineered, smooth haul truck bed liner system offers multifaceted benefits: expedited dump cycles enhance productivity, reduced mechanical strain prolongs equipment life, minimized carryback improves safety, and optimized load capacity leads to significant cost savings. For mining operations aiming to maximize efficiency and safety, such an investment is not just beneficial—it's essential.
Key Benefits of a Well-Engineered Smooth Liner System
- Faster Dump Cycles
- Reduces dump time by 10–15 seconds per load
- Enables 1–3 additional loads per day, per truck fleet
- Translates to up to
273,000 extra tons hauled per year
- Reduced Hydraulic Cylinder Wear
- Full material dump achieved at only 70% bed lift
- Lowers strain on lift cylinders, reducing breakdowns and costly repairs
- Lower Maintenance Costs
- Even wear design minimizes spot repairs
- Fewer welds mean fewer weak points and quicker liner installation
- Less time spent cleaning out carryback material
- Increased Payload Capacity
- Reduced material stickage means trucks haul closer to full capacity
- Decreased carryback increases daily tonnage and overall fleet efficiency
- Improved Safety
- Minimizes risk of stuck material falling during maintenance
- Cleaner dumps reduce manual clean-out, protecting personnel
- Longer Service Life
- Premium materials like SureAlloy® and Vanguard Wear Plate extend liner lifespan
- Durable, low-friction surface maintains performance over time
- Fuel and Operating Cost Savings
- Fewer trips and reduced idling during dumps save fuel
- Case studies show up to $1.9M in savings per truck per year