Maximizing ROI: With Engineered Wear-Resistant Liner Systems
How Engineered Wear-Resistant Liner Systems
Cut Labor and Fuel Costs
In today’s industrial environment—marked by rising diesel prices and a tightening labor market—finding ways to stretch operational dollars is critical. Equipment downtime and excessive maintenance hours aren't just inconveniences—they’re costly setbacks. That’s why more operations are turning to premium engineered wear-resistant liner systems to optimize performance, reduce costs, and extend service life.
Efficiency Starts with Engineering
An engineered liner system isn’t just about protecting surfaces; it’s about improving the entire operational workflow. Systems that are properly designed—using precision 3D laser scanning—ensure that every liner fits seamlessly into equipment like truck beds, slag pots, or material handling buckets.
This technology eliminates guesswork during installation. The liners arrive field-ready, with minimal welding seams and no need for onsite modifications. That means faster install times, fewer man-hours, and reduced risk—all of which translate into measurable cost savings.
ROI Insight: Companies implementing custom-engineered liners have reported labor cost reductions of 30–50% during installation and maintenance windows due to simplified fitment and reduced install complexity.
Material Matters: Why Premium Wear-Resistant Solutions Deliver More
While standard AR400 or AR500 wear plate may be considered the industry baseline, advancements in materials science have introduced far more efficient options. Premium solutions—such as carbide overlay plates—offer dramatically extended service life with thinner profiles.
For example: Replacing a ¾" AR500 plate with a ¼" on ¼" premium carbide overlay plate can:
- Provide up to 20x the wear life
- Reduce overall system weight
- Lower fuel consumption by 3–8%, depending on application
- Decrease stress on hydraulic systems and other moving components
The result? More uptime, increased payloads, and reduced wear on costly components.
ROI Insight: Over the lifespan of a single truck bed or bucket, operators may save $10,000–$50,000+ when accounting for fuel efficiency, reduced maintenance, and extended replacement intervals.
Inventory and Availability: A Hidden Cost Center
Material availability has become a make-or-break factor in maintenance scheduling. Delays due to unavailable parts or materials can derail entire maintenance windows, causing unplanned downtime and bottlenecks in production.
When choosing a wear liner partner, ensure they not only use advanced design tech like 3D scanning but also maintain
inventory of high-quality wear-resistant materials. Companies that manufacture their own wear materials or stock key products can deliver faster and more reliably.
The Bottom Line
Choosing the right engineered liner system isn't just about durability—it's about total system efficiency. When properly implemented, these solutions can:
- Reduce labor hours and maintenance downtime
- Extend service intervals
- Improve equipment payload and fuel efficiency
- Minimize component wear and stress
- Boost overall production capacity
In short, it’s a strategic investment that pays for itself—often many times over.
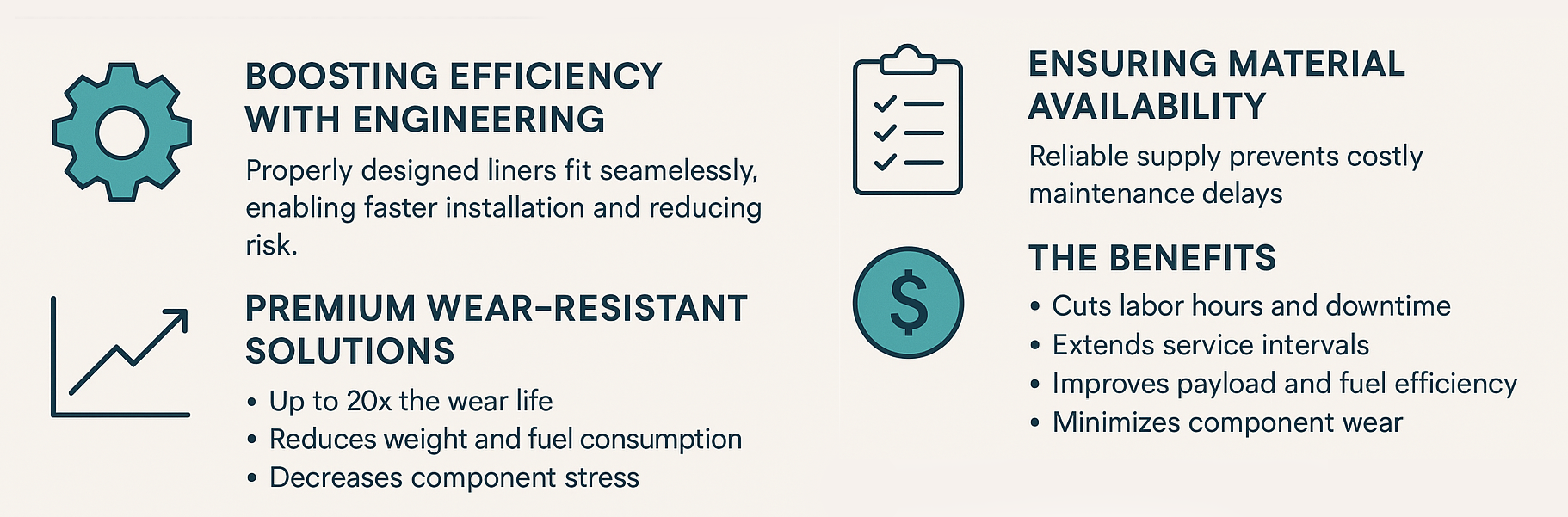