Boosting Combustion Efficiency and Heat Rate: How Mill Modernization Pays Off
Improve Heat Rate with the SAS Global Pulverizer Modernization Programs and Complete Turnkey Solutions
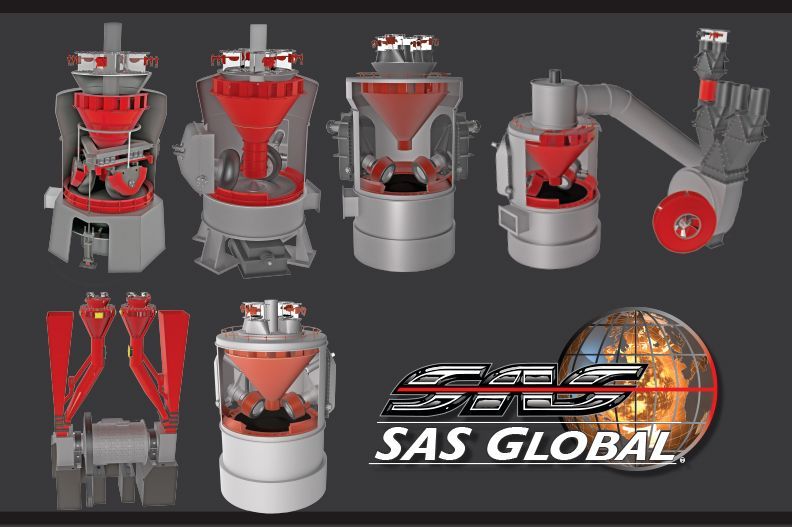
In today’s competitive and environmentally-conscious power generation market, efficiency is more than a goal—it’s a necessity. One of the most effective ways to improve operational performance in coal-fired power plants is by modernizing the coal mills, which are often overlooked but directly tied to combustion efficiency and heat rate.
SAS Global’s pulverizer modernization program is a turnkey solution that optimizes mill performance to increase capacity, improve fineness, balance fuel pipes, and enhance air/fuel ratios. The result? Better combustion, longer component service life, and lower heat rates—translating directly to reduced fuel costs, lower emissions, and improved market positioning.
Why Heat Rate Matters
Heat rate—the amount of energy (in BTU) required to generate one kilowatt-hour (kWh) of electricity—is a critical metric of a coal plant’s efficiency. Lower heat rate means less fuel burned per kWh, which leads to:
- Significant fuel savings
- Lower operating costs
- Reduced emissions (CO₂, SO₂, NOₓ, Hg)
- Improved environmental compliance
According to the U.S. Energy Information Administration (EIA), coal-fired plants in the least efficient quartile (Q4) have the highest potential for heat rate improvement, with estimates showing improvements ranging from 6% to over 13% depending on plant type. Even modest improvements of 1–2% can result in annual fuel savings in the millions of dollars.
How Mill Performance Affects Heat Rate
Mill performance and combustion efficiency are inseparable. Factors like fineness, fuel pipe balance, and air/fuel ratios directly influence boiler performance. An imbalanced mill leads to poor combustion, higher LOI (loss on ignition), and an increased heat rate.
Modernizing the mills helps to:
- Improve coal fineness, ensuring more complete combustion
- Balance fuel distribution between pipes for even burner operation
- Optimize air/fuel ratios to reduce excess air and maximize flame temperature
- Lower LOI and unburned carbon levels in ash
SAS Global’s custom-engineered modernization components are designed for each specific mill and application, providing a tailored solution with measurable results.
Case Study: MPS89 Mill Modernization Success
A recent turnkey mill modernization project completed by SAS Global on a 700MW B&W wall-fired unit highlights the dramatic impact of targeted upgrades.
Key Details:
- Unit: 700MW B&W Opposing Wall-Fired Boiler
- Mills: (7) MPS89 Pulverizers
- Previous Contractor: 15-day overhaul per mill
- SAS Overhaul Time: 10 days per mill (33% faster)
Challenges Identified:
- Utility was unnecessarily replacing mill ring seats regardless of condition.
- Lack of awareness from operators on optimal component usage and lifecycle.
SAS Modernization Scope:
- Patented Closed Race Rotating Vane Wheel with Cast Deflector Liners
- SA2000 Classifier Cone and Extension Kit
- High Spin Static Classifier
- Multi-Outlet Diffuser
- Tire Shields, Mill Wall Liners, and more
The overhaul avoided unnecessary costs by retaining healthy components and reinvested the savings into performance-enhancing upgrades.
Results:
- Reduced outage duration and overhaul costs
- Enhanced combustion stability and mill output
- Positive operator feedback and repeat orders
- Improved heat rate following boiler tuning after the seventh mill was completed
Return on Investment: Heat Rate and Cost Savings
Based on EIA projections, plants in the lower quartiles can achieve up to 10% heat rate improvement, with capital costs averaging $0.20 to $0.90 million per MW and O&M costs of $4,000–$20,000 per MW-year depending on plant configuration.
Example ROI Calculation: For a 700MW plant improving heat rate by just
5%, assuming a fuel cost of $2.50/MMBtu and 85% capacity factor:
- Annual Fuel Use (Before): ~52 million MMBtu
- Fuel Savings (5%): ~2.6 million MMBtu
- Annual Savings: ~$6.5 million
Even accounting for capital and O&M expenses, the payback period is typically under 2 years, making modernization a highly cost-effective investment.
Why Choose SAS Global?
SAS Global is a proven leader in pulverizer modernization with a comprehensive,
turnkey approach—from diagnostics and engineering to fabrication and installation. Our solutions are engineered to maximize combustion efficiency and component longevity while minimizing downtime.
SAS Global Offers:
- Baseline diagnostics & testing
- Custom, Patented Mill components
- Turnkey installation & overhaul
- Post-installation tuning & testing
Conclusion
Mill modernization isn’t just an equipment upgrade—it’s a strategic investment in plant performance, emissions reduction, and financial stability. By partnering with SAS Global, coal-fired power plants can unlock the full potential of their combustion systems and realize substantial returns in fuel savings and operational efficiency.
Contact SAS Global today to start improving your heat rate and saving millions in fuel costs.