PATENTED ROTATING VANE WHEEL - MPS SERIES
Modernize Your MPS Mill with the SAS Adjustable Throat
Proven Performance: SAS Rotating Vane Wheel Conversions for MPS Mills
Since the 1980s, SAS Global has been engineering and building Rotating Vane Wheel Conversions for MPS-style mills—combining decades of real-world field testing with advanced computational modeling to continually improve both performance and durability.
Our focus isn’t just on improving mill efficiency—we also design with maintenance access and service life in mind. Each vane wheel can be built from a range of wear-resistant materials, customized to match the specific fuel blend and operating conditions at your plant.
Proven Results Across the Industry
With over 700 vane wheel kits installed across North and South America, SAS Global has a proven track record of success. Many plants that install their first SAS kit quickly schedule full conversions across all remaining mills—a clear sign of the performance and reliability delivered by SAS technology.
Why Power Plants Choose SAS Rotating Vane Wheels
Although each plant has its own unique challenges, the consistent benefits driving these conversions include:
- Improved coal classification and distribution
- Enhanced fineness and combustion efficiency
- Reduced wear and extended service life
- Simplified maintenance with better access to critical components
- Custom-engineered materials matched to your fuel and wear conditions
With SAS Global Rotating Vane Wheel Conversions, you’re not just upgrading a component—you’re investing in a proven performance enhancement tailored to your mill, your fuel, and your plant’s specific operating goals.
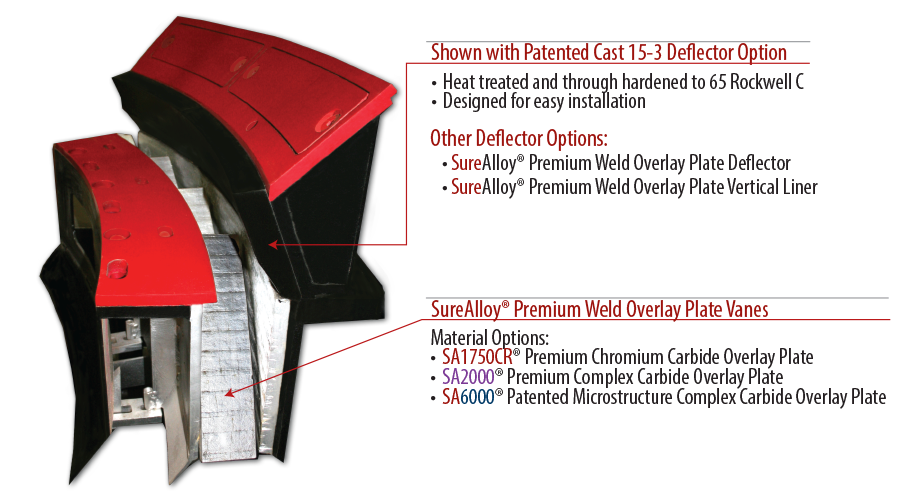
PERFORMANCE BENEFITS:
- Lower Mill Motor Amps: Typical reductions have been 10% to 18%
- Lower Primary Air Flows: The SAS design has adjustable airport, allowing throat air velicities to be adjusted to match the required air mass
- Increased Fuel Drying Capability: The SAS vane/deflector arrangment dries the coal faster by providing a more evenly supported coal bed around the periphery of the bowl.
- Quicker Mill Response Time: An evenly supported coal bed and improved circulation/mixing of hot primary air provides smoother and quicker ramping of the mill.
- Increased Mill Capacity: Having extra capacity is beneficial should a mill be removed from service during peak generation times.
- Lower Maintenance Costs: Even coal flows at lower velocities will improve the life of internal mill components.
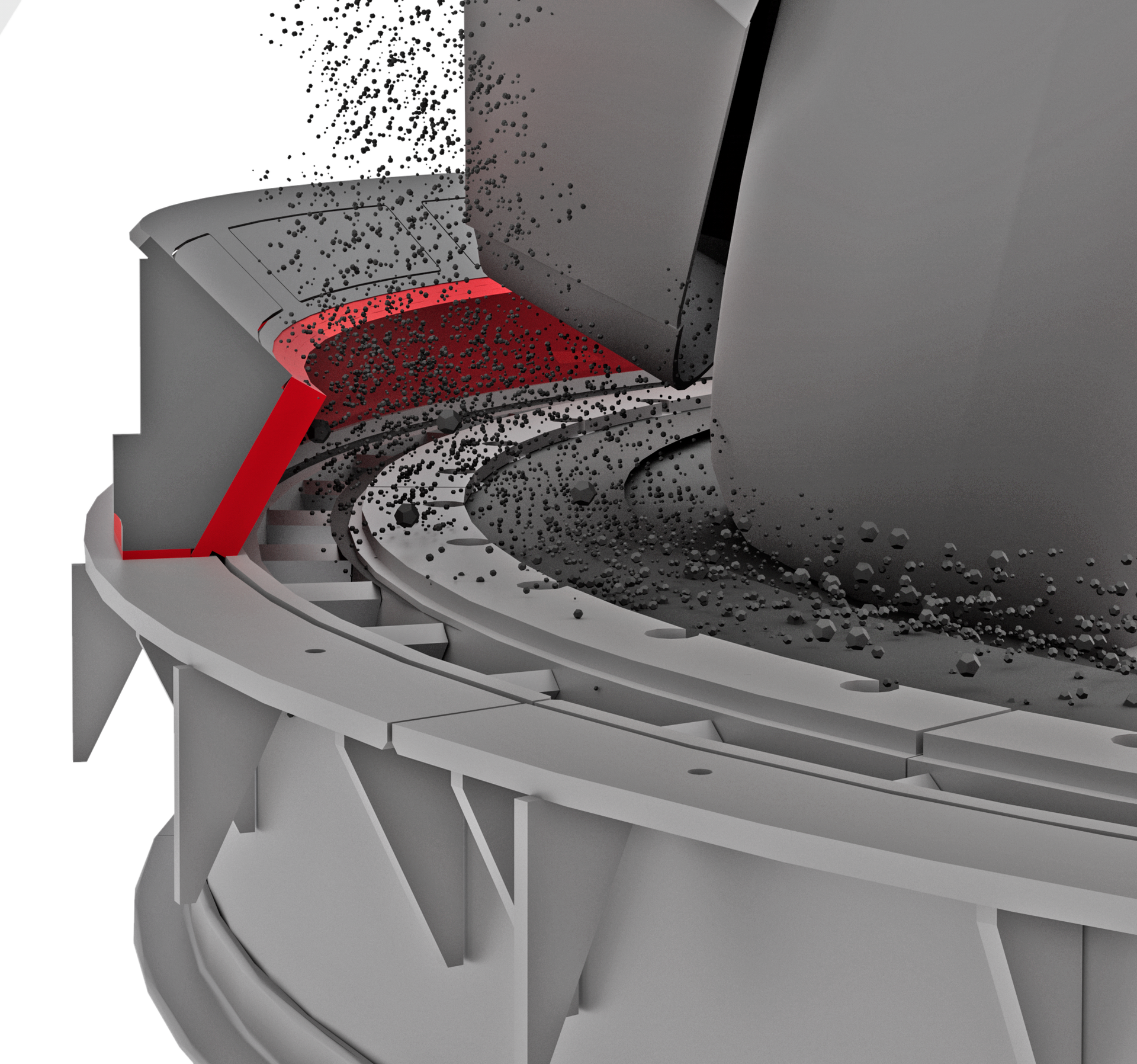